MPO cleaning guidelines are much like those for single-fiber connectors
In November 2020, Fiber Optic Center posted an article on cleaning and inspecting connector ends, Ten Practical Tips for Cleaning Connector Ends. With the article below, we are expanding on that subject to comment on the special requirements of MPO-type multi-fiber connectors.
A brief definition: MPO stands for multi-fiber push-on, and it refers to a family of connectors. MT stands for mechanical transfer, and it refers to the rectangular ferrules that are used in MPO connectors. Depending on the number of holes in the ferrule, an MPO mated pair can connect from four to more than 32 fibers.1
Due to the complexity of terminating multiple fibers in one device, MPO connectors are almost always mounted in an assembly factory. Field operations mainly consist of attaching prefabricated MPO assemblies to panels and other hardware. For both factory and field, the requirement to clean and inspect all fibers means rigorously following well established procedures.
One key difference between MT and cylindrical ferrules is the material. MT ferrules are plastic. Most connectors for single-mode and multimode communication networks use ceramic ferrules.2 The MT’s plastic materials may be more susceptible to scratches and other defects, but the plastic chips or particles will not scratch the glass fibers. Generally, the plastic ferrules can be cleaned with the same wet or dry procedures as ceramic ferrules. Lint-free wipes and swabs, compressed air, isopropyl alcohol, and other cleaning materials are all suitable for use with the thermoplastic MT ferrule materials, as they are with ceramics.
There are, however, several characteristics of MT ferrules that differ from those of standard cylindrical ferrules and have implications for cleaning and inspection:
- larger rectangular ferrule – cleaning and inspection tools must have fixtures for the MT ends;
- guide-pins and holes for mated-pair alignment – require special cleaning tools and procedures
- multiple fiber ends in each ferrule – each fiber must be cleaned and inspected;
- fiber protrusion – the assembled ends are polished so that the fibers extend 1.0 to 4.0 µm beyond the MT ferrule’s polished end face.2
Cleaning-product manufacturers offer versions for MT ferrules
Widely used cartridges and other connector cleaning tools are available with features to accommodate the larger MT ferrules and guide pins. The cassette-style cleaning cartridges, for example, are designed with recessed pathways for the male MT’s protruding guide pins to pass through while the cartridge’s cleaning surface passes over the ferrule end face. Pen-type cleaners also have versions designed for the rectangular MT end face.
Note that MT ferrules are always the same size, even for MPO connectors with different fiber counts. That is, the rectangular end face has the same length and width dimensions. This means that the same cleaning tools and fixtures can be used for all MPO connectors, regardless of the number fiber ends. Some of the cleaning-tool manufacturers offer separate versions for male and female MT ferrules, but in many cases, the same cleaning product can be used for both male and female ends.
Remember the guide-pins and holes
MT ferrules require cleaning and inspection steps that are not necessary with cylindrical types – steps to assure the guide pins and guide-pin holes are clean or free from obstruction. On the other hand, connections with cylindrical ferrules require that the split-sleeve alignment units are cleaned and inspected. MPO connectors with MT ferrules do not use such sleeves. In a sense, the need to clean and inspect the split sleeves is replaced by the need to clean and inspect the guide pins and holes.
With MPO connectors having fiber protrusion specified in a range of 1 to 4 µm, a contaminating particle in a guide-pin hole, say a particle measuring just 1 or 2 µm, could prevent a good physical contact between some of the fiber ends. In the factory, procedures using compressed air and solvent-based cleaning systems can assure the guide-pin holes are clean when the assemblies are bagged and shipped for field use. In the field, the installers typically assume the guide-pins and holes are clean when the assemblies are taken out of the bags. For subsequent mating cycles, field technicians should use brushes, compressed air, or swabs with solvent to clean the guide pins and holes. Brushes made in sizes specifically for cleaning guide-pin holes are available.
The microscopes used for inspecting fiber ends in the field typically have magnification of 60, 80, 100, or 200 X. This level of magnification is too strong for the guide-pin holes. For inspecting the guide pins and holes in the field, an inexpensive 10 X loupe is fine. Assembly factories often have automated systems for fiber-end inspection, and the system suppliers offer adapters and fixtures for MT ferrules. Some of these systems are similar to field microscopes, with magnifying optics ranging up to 200 or 400 X, and even higher in some cases. Other factory systems use interferometry for fiber-end inspection. But as with field inspection, assembly production in the factory environment requires a separate step to check the guide pins and holes.
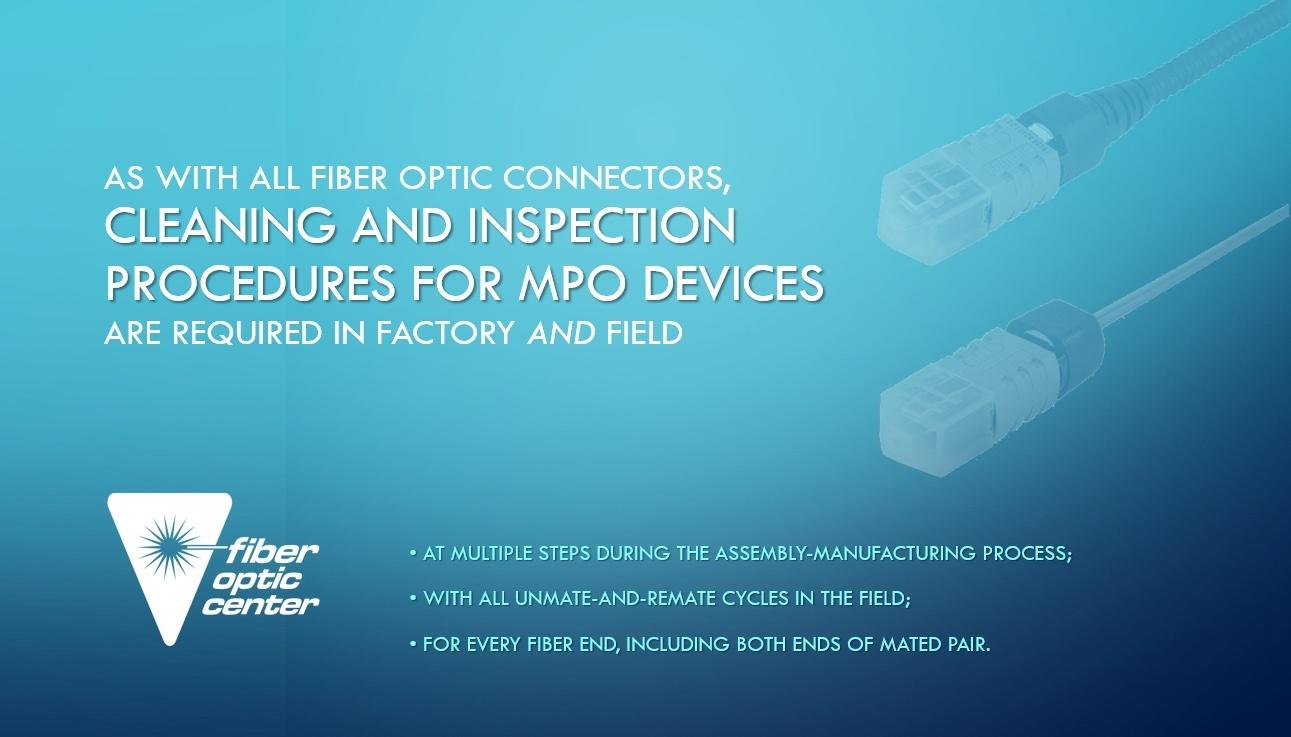
Conclusions
MT ferrules require rigorous procedures for cleaning and inspection – the same as cylindrical ferrules. This is true for factory assembly production and for network installation and operations. In the factory, thorough rinsing and cleaning is required after each assembly and polishing step, and final inspection must include the guide pins and guide-pin holes as well as the fiber ends. Contaminants in the guide-pin holes potentially could interfere with the way fiber ends contact each other in a mated pair of MPO connectors, and this could cause problems with insertion loss, return loss, or other performance factors.
There is a wide selection of products for cleaning and inspection – ranging from handheld tools to bench-top instruments. Field technicians can use dry lint-free cleaning products, such as cartridge- or pen-type cleaners that are designed for use with MT ferrules. Instruments for assembly factories, including automated systems, are available with fixtures and adapters for MT ferrules and MPO connectors. For assistance in specifying, selecting, and using various cleaning and inspection products, please contact FOC.
____________________