Domaille Engineering ABRASAVE ‘C’ CS/APC 16-Port Polishing Fixture
View the demonstration above and request a quote today.
Transcript
AbraSave polishing fixture line. This fixture line is guaranteed to reduce your polishing time up to 50% and double the useful life of your AbraSave film. These amazing improvements are made possible by a concept we call unique path technology. Whether it is an LC, SC or MT connector, round or square, a fixed polishing fixture or pivoting all standard polishing fixtures have connector boards that are equally aligned around the center of the fixture on the same radius and with the same angular relationship. Traditionally, they have been produced this way for ease of manufacture. The drawback being that all the ports on any polishing fixture follow the exact same path causing premature wear to the AbraSave film. This reduces the useful life of the film and significantly lengthens polishing time. A close look at the new AbraSave fixture reveals that the portholes are not on the same radius and that the angular spacing is also not even.
The unique path technology that is used in the new AbraSave fixture is designed to mathematically put each connector on a different path as it goes across the polishing media. On the MT fixture, This is taken a step further, you can see that each port is slightly candid. This design allows each of the 12 fibers within the single connector to have its own unique path. This is the Domaille APM-HDC-5100 polishing machine, the finest optical fiber polishing machine on the market, we have replaced the AbraSave film with a clean white label to show the effects of the AbraSave fixture we’ve replaced connectors with markers and we’ll set the machine to polish using a standard fixture. Look at the pattern on the label. You can see that with the same radius and angles all the connectors follow the same path which will inevitably cause premature wear on the AbraSave film adding to the polishing time needed to achieve the desired results. Efficiency is lost and lengthen polishing times and cost is added because the AbraSave film must be replaced even though much of the film is unused.
Now we’re running the new AbraSave fixture using the same polishing parameters. Here is a side by side comparison of the wear pattern left by a standard fixture and an AbraSave fixture both run for 60 seconds at 120 rpm. Even in just 60 seconds, it is easy to see the dramatic difference in wear pattern gained by our unique path technology with standard fixture uses less of the available film and keeps following the same pattern causing premature wear. The AbraSave fixture covers nearly 20% more of the film surface placing the polishing points on fresher AbraSave film so polishing occurs quicker. This comparison makes it easy to understand how polishing times are reduced by up to 50% and the life of the AbraSave film is extended by up to 100%. From a business standpoint, the AbraSave fixture line brings a lot to the table. Quicker cycle times mean more connectors can be polished with the same resources no need to add personnel or invest additional capital to increase revenue. There is less work in progress, less rework of connectors and increased inventory turns.
With extended film life operating expenses are decreased. All our customers have been reporting a 3-9 month return on investment from this technology. Many are changing out their entire production line to the money and time saving of AbraSave solutions available in both round and square fixtures. The AbraSave technology can be applied to any style connector and can be adapted to almost any competitor’s polishing machine.
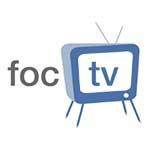